Journal
Metals of the Book of Mormon
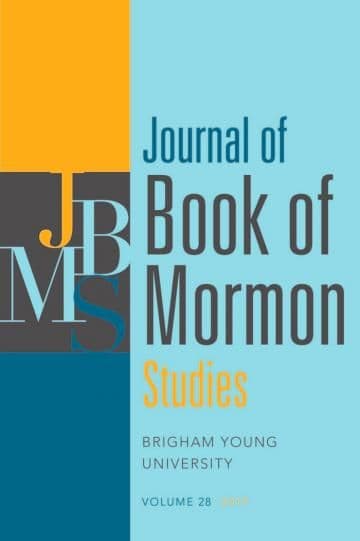
Title
Metals of the Book of Mormon
Publication Type
Journal Article
Year of Publication
2000
Authors
Phillips, Wm. Revell (Primary)
Journal
Journal of Book of Mormon Studies
Pagination
36-41, 82
Volume
9
Issue
2
Abstract
For three weeks in February 2000, a team of BYU geologists worked in coastal Dhofar, focusing on geological formations that could have produced the metals needed by Nephi for making tools to build a ship. This article discusses the ores and processes that Nephi would have employed and considers the possibility that the coast of Dhofar may be a candidate for the location of Nephi’s shipbuilding.
Although Nephi’s tools were most likely made of iron or steel, bronze remains a possibility. The making of brass or bronze requires the creation of a copper alloy, and examples of such alloys are found in both the Old World and the New World. The nature of the alloys differed depending on the minerals available.
Metals of the Book of Mormon
Wm. Revell Phillips
A small team of BYU geologists working on the south coast of Oman recently gave added credibility to the Dhofar coast as the land “Bountiful” that marked the end of Lehi's trail (1 Nephi 17:5). There, commanded by God to build an oceangoing ship, Nephi asked divine help to find ore so he might make tools for this seemingly impossible task. Considering the technology of Nephi's time, his tools could have been either bronze or iron, though iron is the more likely, as we shall see.
Although the northern regions of Oman were once famous for their copper deposits, the Dhofar was considered barren of metallic ores and has never had a mining industry. The BYU geologists, however, discovered two small iron occurrences on the south Oman (Dhofar) coast. Neither would sustain an iron industry, but either could yield tons of high-grade iron ore, more than adequate for Nephi's needs.
Several logical sites have been proposed for Lehi's camp and Nephi's shipbuilding. The inlet bay at Salalah, on the verdant Dhofar Plain, was proposed by Lynn and Hope Hilton;1 the peaceful and pristine Wadi Sayq, where it enters the Arabian Sea a few kilometers east of the Yemen border, has been championed by Warren and Michaela Aston;2 and Richard Wellington and George Potter3 make a case for Khor Rori, an Iron Age port about 40 kilometers east of Salalah and 20 kilometers west of Mirbat at the east end of the Salalah Plain. The exact site is probably unimportant, unknown, and likely to remain so; however, wherever Nephi built a ship in the land Bountiful, we now know he was within a few kilometers of a usable deposit of good iron ore.
The Dhofar coastal strip, only a few miles wide, is blessed with abundant rainfall during the monsoon months when dry wadis may become raging rivers and the land becomes green with dense, tropical vegetation—certainly a blessed relief from the harsh desert and the maze of barren canyons and dry wadis northward. The Dhofar coast is still noted for its fruit orchards and honeybees.4 The Salalah Plain is a small oasis of agricultural land isolated by the Arabian Sea on the south and desert highlands to the north. Within this very limited area, the writer observed groves of papaya, bananas, mango, coconut, and other common fruits, most of which were probably introduced to the Dhofar long after Nephi's brief sojourn there. Native fig trees, date palms, and coconut palms, however, may have provided abundant and durable fruit for Nephi's long sea voyage.
Fieldwork
Intense LDS interest in the land Bountiful began with Hugh Nibley's publication of Lehi in the Desert in 1952.5 Interest was kept alive by the Hiltons and Astons, finally attracting the attention of FARMS.
In February 1998 S. Kent Brown, director of Ancient Studies at BYU, assembled a diverse four- man team of BYU scientists to explore the Dhofar coast.6 Thus began a welcome and long-overdue cooperation effort between science and religion at BYU. Brown and his team (Terry B. Ball, botany; Arnold H. Green, ancient history; David J. Johnson, archaeology; Wm. Revell Phillips, geology) explored the Dhofar area for a week. Each team member learned from the others and formulated a research project that would involve his own discipline and academic department in a meaningful study in this fascinating land. The objectives of each project were for team members to be completely professional, to produce research beneficial to the Omani government and its scholarly community, to foster a cooperative effort involving scholars from the host country, and to conduct a scientific mission of goodwill for BYU. Spinoffs from each project may well reward the participants and supporters with enriched understanding of the sojourn of Lehi and his family in the land Bountiful.
The geology team was assembled by the writer in the summer of 1998 and began preparations for fieldwork in the Dhofar. The team members were Jason G. Aase, a graduate student in geology at BYU; Eugene Clark, a former Exxon and Standard Oil geologist in Oman; Ronald A. Harris, a BYU professor of geology (earth tectonics); Talal Al Hosni, a graduate student in geology at Sultan Qaboos University in Oman; Jeffery D. Keith, field director and a professor of geology (economic geology); and Wm. Revell Phillips, a BYU emeritus professor of geology (mineralogy).
For three weeks in late February 2000, the team members concentrated their efforts in the coastal Dhofar and focused on the rocks that would most likely yield metallic ores of possible value to the Omani economy and that could have been used by Nephi of old for making tools to build a ship. Their effort was rewarded by exciting discoveries that will enrich, broaden, and perhaps even redirect the knowledge and understanding of the geology of Oman. This scholarly work will be reported in appropriate professional journals and presented at an international conference on the geology of Oman to be held in Muscat in January 2001.
By his own admission, Nephi needed timber for building the ship and metal tools for its construction. While the search for timbers falls more to the botany team, the geologists made a short detour to the coastal port of Sur, which boasts the only shipyard in Oman still building traditional Arab dhows by hand. We are uncertain of Nephi's vessel design and the materials he used in constructing it. The modern Omani workmen, however, say that local acacia trees, widely scattered over the arid Omani landscape, have trunks about the right size and curvature for a ship's ribs. The keel and outer planking, however, require long, straight, dense timber, apparently not presently available near Sur. Teakwood, they say, is ideal for shipbuilding and is imported from nearby India to the shipyard at Sur, where the huge logs are transported by narrow-gauge railway cars and fed into large horizontal band saws.
The shipping lanes between India and Africa, with a stop in southern Arabia, have transported teak for centuries.7 Perhaps Nephi obtained teak timbers by trading frankincense, honey, or some other local product at the busy port of Kane, in Yemen, or Khor Rori, in the Dhofar, if local timber was not adequate. Khor Rori, dating to at least Roman times,8 and Kane, dating somewhat earlier, were the principal ports for shipping frankincense from the Dhofar.9 Nephi recorded only that he and his brothers “did go forth” for timber (1 Nephi 18:1), indicating that the necessary timber was not exactly where he was.
Iron Ores
In the context of Nephi's day, there were only two reasonable options for a metal to make tools: bronze and iron. Nephi lived at a time when iron and simple steel had become commonplace in Jerusalem, yet bronze was retained for special purposes like casting. Bronze was softer and generally inferior to steel for toolmaking, and producing it required a source for its components, copper and tin. Only minor traces of copper minerals have been reported in the Dhofar,10 and tin is unknown there. Of course, tin and copper might possibly have been trade items on the India-Africa trade route suggested above.11 Because the geologists found no trace of copper or tin along the Dhofar coast, they searched for iron deposits sufficient for ancient toolmaking.
The Dhofar has no economic ore deposits capable of sustaining a metal industry. It is almost completely covered with a thick sequence of Cretaceous and Tertiary limestones, essentially devoid of concentrations of any metal. Only east of Mirbat are the limestones eroded away to expose a broad plain of the Precambrian “basement complex” (i.e., very old igneous and metamorphic rocks). This represents an erosional window into the African-Arabian shield, about 60 kilometers long and 30 kilometers wide, lying between the Arabian Sea and the steep limestone face of Jabal Samhan. We reasoned that any significant concentration of metallic ore minerals should be exposed in this basement complex.
A small area west of the Salalah plain held a promising surprise. Gene Clark recalled seeing, several years ago, a very small exposure of early Paleozoic sediments and the earlier Precambrian rocks at the mouth of Wadi Nharat, only a few kilometers east of Wadi Sayq. Arriving at the tiny port of Rakhyut, the team hired a fishing boat and, instead of sailing west to Wadi Sayq, sailed east to Wadi Nharat. In the wadi the early Paleozoic Al Hota formation of greywacke rocks was cut by thin, igneous dikes of a light-colored, iron-stained rock that proved to be a fine-grained carbonatite composed largely of calcite (CaCo3) and siderite (FeCo3). The dikes sometimes widened to expose central pods of nearly pure hematite (Fe2O3). One pod, for instance, measuring about 8 feet by 10 feet in outcrop, would yield several tons of high-quality iron ore, more than enough for a few shipbuilding tools. This rich hematite ore would have much associated carbonate (i.e., limestone) impurities, like that added, as a flux, in modern steel furnaces. The carbonate does not react with the iron or lower its melting point, but it does combine with, and lower the melting point of, common silicate impurities to form a fluid molten slag. This carbonate may have enabled someone like Nephi to reduce the hematite to iron at a lower temperature and to forge from the iron a more fluid slag than would have been possible without the carbonate flux.
East of Mirbat, the geology team began its exploration of the broad, igneous-metamorphic basement complex at the east end of the broad Salalah plain, about 75 kilometers east of Salalah and 150 kilometers from Wadi Nharat. Here, almost on the outskirts of Mirbat, they made their most exciting and significant geological discovery. This discovery will be the central theme of the professional reports and publications that the team expects to release in the coming year. Associated with this discovery were, again, carbonatite dikes rich in the iron-carbonate siderite, which weathers to a gossan-like mass of goethite-limonite ore (Fe2O3.nH20)—not enough for an iron industry, but quite adequate for forging a few tools. This site is about 10 kilometers east of Khor Rori. Hence, regardless of whether Nephi built his ship at Salalah, Wadi Sayq, Khor Rori, or any other site along the Dhofar coast, he was within a few kilometers of quality iron ore easily accessible from the sea.
Ancient Smelting
Let us consider what Nephi might have known about the smelting and working of iron and steel. The traditional Iron Age began in the eastern Mediterranean about 1200 B.C. However, manufactured iron objects appear much earlier in the human record. Native iron is unknown in nature, except as meteorites that fall to the earth's surface from outer space. Many of the earliest worked iron objects are meteoric iron, as determined by their high nickel content and unique microstructure. The early Hittites spoke of “black iron from heaven,” and in ancient Egypt it was “iron of heaven.”12
Iron is, of course, subject to disintegration by rusting, so we might expect most ancient iron to be lost to rust. Nevertheless, at least 14 remnants of fashioned iron objects have been dated to before the Early Bronze Age (3000 B.C.).13 Only five of these have been chemically analyzed for nickel, and only three of them appear to be worked meteoric iron. The two remaining objects are smelted iron, one dated 3500-3000 B.C. and the other about 5000 B.C.14 Thirty iron objects are known from the Early and Middle Bronze Ages, and about half of the analyzed objects are smelted iron.15 Most, if not all, of the 18 analyzed iron objects of the late Bronze Age appear to be meteoric.16
The Old Testament and Pearl of Great Price introduce Tubal-cain as “an instructor of every artificer in brass and iron” (Genesis 4:22; Moses 5:46). The name Cain (qayin) in Hebrew means “smith,”17 and “Tubal” is a prominent iron locality cited in Ezekiel 27:13. Since Tubal-cain is the sixth-generation descendant of Cain and Noah is the eighth generation from Seth, these scriptures imply a date for ironworking prior to the great flood and place Tubal-cain over two millennia before the beginning of the so-called Iron Age in the eastern Mediterranean (1200 B.C.).
Although iron was known and smelting techniques were practiced, by intention or accident, before 1200 B.C., the dawn of the Iron Age saw a sharp increase in the number of iron objects, and iron gradually replaced bronze, first as farm tools and then as weapons. Two or three centuries earlier, the Hittites migrated to central Anatolia, perhaps bringing with them the secret of iron smelting from the “east.”18 Some historians believe the Hittites exploited their monopoly of iron for military advantage, and Hittite kings wrote about iron in correspondences sent to monarchs in Assyria (Shalmaneser I) and Egypt (Ramses II).19 About the beginning of the Iron Age, Hittite lands were overrun by a wave of the indeterminate “Peoples of the Sea” and the secret of iron passed to the Philistines, a branch of those mysterious people.20 Other than among the Hittites, the only serious use of iron before 1000 B.C. was in Cyprus and Palestine, among the Philistines and their allies, the Canaanites.
Iron came late to Israel, and its enemies pressed their advantage. “Now there was no smith found throughout all the land of Israel; for the Philistines said, lest the Hebrews make them swords or spears: But all the Israelites went down to the Philistines, to sharpen every man his share and his coulter, and his axe and his mattock” (1 Samuel 13:19-20). “And the Lord was with Judah, and he drave out the inhabitants of the mountain; but could not drive out the inhabitants of the valley, because they had chariots of iron” (Judges 1:19). “And the children of Israel cried unto the Lord: for he [Jabin, king of Canaan] had nine hundred chariots of iron: and twenty years he mightily oppressed the children of Israel” (Judges 4:3). By the time of Israel's kings (1000 B.C.), Israel had mastered the technology of iron and there were smelting furnaces at Ezion-Geber at the head of the eastern arm of the Red Sea.21
Iron Making
The beginning of the Iron Age (1200 B.C.) was a period of great turmoil in the eastern Mediterranean. Trade routes were disrupted and Bronze Age civilizations collapsed (e.g., the Hittite Empire, Mycenaean Greece, New Kingdom Egypt, and the Ugarit Kingdom).22 Tin was always expensive (15 to 18 times the price of copper), but with the loss of the tin trade, the price of bronze must have soared to hasten the conversion to iron. Iron ore was abundant and cheap, but the technology of smelting and working iron was different and difficult. Iron could not be melted and cast like bronze. The melting point of iron is 1535° C (2795° F), which was unattainable in primitive charcoal furnaces, and it had to be worked in the solid state, which was labor-intensive and time-consuming.23
China has no tradition of hammered iron, but as early as the eighth century B.C. the Chinese were able to melt and cast iron into molds to produce “pig iron.”24 High-temperature metallurgical furnaces may have developed in parallel with furnaces for the manufacture of Chinese porcelain, which required similar temperatures and which was not duplicated in Europe before the 18th century. West of India, however, all iron was forged wrought iron before the Industrial Age in Europe.25
In the New World, the Jaredite record makes early reference to iron (see Ether 11:23), and Shule, Jared's great-grandson, was said to be a maker of steel swords (see Ether 7:9). Because Jared and his brother departed the Near East for the Americas at the time of the great tower and the confounding of languages (see Ether 1:33), scriptures again note (the other instances being Genesis 4:22 and Moses 5:46) a date for iron and steel millennia before the Near East Iron Age. John L. Sorenson cites 16 authors who claim to have found ancient iron objects in the New World.26 Most of these finds, however, are by amateur archaeologists who do not distinguish meteoric iron and may have no credible way to fix the antiquity or authenticity of their finds. Jaredite swords discovered by the explorers of King Limhi were said to be “cankered with rust” (Mosiah 8:11). One might cite this as evidence that the Jaredite swords were, indeed, of iron or steel; however, sacred texts may occasionally use rust as a metaphor for other forms of decay and corrosion. For example, the New Testament speaks of the “rust” of cankered gold and silver (James 5:3). Although research is very limited and incomplete, modern archaeologists have reported no artifacts of “smelted” iron in the New World of certainty earlier than the Spanish conquest.27 Matthew Roper notes “no evidence from Mesoamerica archaeology or tradition to indicate the use of metal in the manufacture of swords,”28 and Heather Lechtman writes, “There are indications that iron would not soon have been added to the Andean repertoire of metals.”29
Lehi's journey, beginning about 600 B.C., falls well within the Mediterranean Iron Age and well after David and Solomon made smelted iron a common metal in Israel. Lehi or Nephi may have brought with them considerable knowledge of the smelting and forging of iron and steel and a few objects of these metals (e.g., Laban's sword and Nephi's bow). It would be possible and logical for Lehi to include at least an iron hammer and ax among the “provisions” he prepared for his journey (1 Nephi 2:4). Nephi states: “And I did teach my people to build buildings and to work in all manner of wood and of iron, and of copper, and of brass, and of steel, and of gold, and of silver, and of precious ores” (2 Nephi 5:15). He implies knowledge in matters of smelting and working a variety of metals, and when required to make shipbuilding tools, he asks for divine help in finding ore but seems to know how to proceed from there (see 1 Nephi 12:8-11). Nephi may have learned these skills from the smiths in Jerusalem or from his multiple journeys between Jerusalem and the Red Sea, which required him to pass repeatedly through southern Wadi Arabah, the principal site for mining and smelting of both copper and iron in ancient Israel. He may have learned from the local smiths of the Dhofar or from the Indian traders that passed through nearby trading ports, and he would not have been the first prophet to be instructed by divine beings. Nephi struck stones together to make fire, built a presumably simple pit furnace, and constructed a bellows of animal skins to blow air into the glowing mass of charcoal and ore (see 1 Nephi 17:11). Bellows of skins are depicted in ancient Egyptian tomb paintings and were in common use in Palestine and throughout the Near East from the second millennium B.C.30 Nephi's smelting furnace almost certainly never reached the melting point of iron (1535° C or 2795° F), but it didn't need to.
When air is introduced into a hot mixture of iron oxides and charcoal, carbon from the charcoal combines with oxygen from the air to form carbon monoxide, which is a reducing gas. This gas filters upward through the charcoal-ore mixture, removing oxygen from the iron oxides to form carbon dioxide; and tiny crystals of iron, freed of its oxygen, filter downward to accumulate at the base of the fire pit as a gray, spongy mass called a “bloom” or “sponge iron.” This form of iron reduction, called the “direct process,” begins at about 1200° C (2192° F), which is possible in a simple charcoal furnace. Although the bloom is not molten, silicate impurities in the ore form a molten slag (see 1 Nephi 17:16) that floats to the top to shield the hot bloom from the oxygen and cooling effect of the air above.31 The white-hot bloom can be withdrawn from the furnace and hammered (“forged”) to squeeze out remaining slag and to weld, or compress, the iron crystals into a solid mass called “wrought iron.”32 Iron produced by this direct process is quite pure (99.5 percent). It is softer and more malleable than good bronze and cannot be hardened by any amount of additional forging.33 Wrought iron is not suitable for tools or weapons, and added forging drives more slag from the iron, making it even more malleable. Long heating of the wrought iron in direct contact with glowing charcoal, however, causes carbon atoms to diffuse into the outer layers of the iron, creating a simple form of steel (martensite).34 This process is called “carburizing,” and repeated carburizing and forging produce an outer layer of steel that can be very hard and sharpened to a fine edge. The iron is said to be “case hardened,” and repeated sharpening will remove the carburized steel. In antiquity, all swords were not created equal. Common soldiers fought with inferior weapons that might dent and bend, but kings wielded swords of special steel, each created by a skilled smith after days or months of hard, hot work at his forge (e.g., Excalibur). The sword of Laban, said to be of “most precious steel” (1 Nephi 4:9), was perhaps one of those special swords.
Today we know that the smiths of Damascus fused together thin layers of carburized steel to form a single blade. Repeated forging produced a visible wavy pattern (“watering”) of carbon-rich and carbon-poor layers visible in the famous Damascus steel.
In a different process, plunging hot steel into water (“quenching”) increases its hardness, but the metal becomes brittle and tools and weapons made from it may break. Reheating to moderate (“red”) temperature and slow cooling (“tempering”) relieves stress in the quenched steel, making it less brittle with little loss of hardness.35
It is important to note that the direct process of iron reduction, forging, carburizing, quenching, and tempering were technologies known throughout the Near East of Nephi's day. All were possible for a learned or inspired man using a simple pit furnace with bellows and a simple forge. These techniques changed little for the arms makers of the Christian crusades or, indeed, for the blacksmiths of the pioneer communities of the American West. Nephi evidently knew all that he needed to know about smelting ore and producing metal tools. What he needed was to learn where he could find a deposit of iron ore. With the Lord's help he found one. Our geologists, too, found two deposits of iron ore in the broad area we believe to be the land Bountiful.
Copper, Bronze, and Brass
Although Nephi's tools were most likely made of iron or steel, bronze remains a possibility. Thus a review of the development of copper and its alloys may be in order and of special interest to readers of the Book of Mormon.
Most copper artifacts dated to before 5000 B.C. are of native metallic copper.36 However, copper was the first metal to be smelted from its secondary ore minerals,37 mostly malachite and azurite, and smelting slags from central Anatolia (Qatal Huyuk) have been dated to as early as 6000 B.C.38 In the Near East native copper is found in a belt from northwest Anatolia to northern Iraq, with a second major source at the Talmessi Mine in Iran. The earliest copper mining appears near Ur before 4000 B.C., and copper was smelted at Ur by 3500 B.C.39 Sea trade between Mesopotamia and Magan (northern Oman) brought impure copper ingots, via Dilmun (Bahrain), up the Euphrates River to Mari, in Sumeria, where the copper was refined.40 This trade continued until about 1700 B.C., when copper mining on Cyprus began in earnest.41
Palestine had little or no native copper, and the metal was relatively rare there in the Bronze Age but became more abundant about the time of Abraham (Middle Bronze Age, about 2000 B.C.). Copper was seriously mined, as secondary carbonates and silicates, and smelted at Feinan in Wadi Arabah by the kings of Israel.42 These colorful, secondary minerals, largely malachite and chrysocolla, are sold to modern tourists as “Elat Stone.”
In the Americas artifacts of hammered native copper in the Lake Superior region date from 3000 B.C.43 Complex and sophisticated metallurgical technologies in the pre-Columbian New World, however, are presently recognized only in the Andes Mountains of Peru and Chile,44 where copper was smelted from rare copper arsenides, sulfates, and chlorides.45 Smelted copper is not presently recognized before the first century A.D.,46 when armaments of cast copper appear (e.g., mace heads, spear points, thrower hooks).47
In the modern world, brass is an alloy of copper and zinc, and bronze is an alloy of copper and tin. Understanding the copper alloys of the ancient or medieval world, however, requires an explanation.
The first copper alloy (Early Bronze Age, about 3500 B.C.) was arsenic-copper, sometimes called “arsenic-bronze,” and was probably produced by accident.48 Copper minerals of the Talmessi Mine were closely associated with arsenic minerals, and smelting likely produced an unintentional alloy49 that melted at lower temperatures than pure copper and was more fluid and easier to cast.50 The new alloy, if recognized as such, was not distinguished with a new name, and the Hebrew word non: and Greek word calkoj~ were applied to both copper and the new arsenic-copper alloy.51 Arsenic was soon a deliberate addition to smelted copper, but before the Middle Bronze Age (2000-1600 B.C.) in the Near East, a tin-copper alloy had largely replaced the earlier arsenic-copper alloy.52 Tin-copper was far superior and was also absorbed by the Hebrew and Greek words noted above. No new word was created to distinguish this new copper alloy.
The zinc-copper alloy may also have been formed by accident, because the common secondary minerals of zinc (smithsonite and hemimorphite) may be closely associated with the common secondary minerals of copper (malachite, azurite, and chrysocolla) in weather-altered, near-surface deposits. Normal smelting of zinc ore does not yield metallic zinc, but smelting a mixture of secondary minerals of zinc and copper together may yield a zinc-copper alloy. Deliberate zinc-copper did not come into use before Roman times, and earlier accidental examples of this alloy are extremely rare.53 This new alloy, too, was absorbed by the existing Hebrew and Greek words for copper, and the Latin word aes or aeris stood for copper and both of its major alloys.54
In antiquity the words bronze and brass did not exist. Brass is an English word derived from braes (Old English) and bres or bras (Middle English) about 1200 A.D.55 In the language of Tudor England, brass stood for any copper alloy, and the King James Bible uses the word in that context.56 Joseph Smith, favoring the King James Bible, translated the Book of Mormon using brass in the same manner. In a ew verses of the Old Testament the Hebrew word for copper is even translated “steel”57 (2 Samuel 22:35; Job 20:24; Psalm 18:34; Jeremiah 15:12) and “amber” (Ezekiel 1:4, 27; 8:12).
The word bronze did not come into use before the 18th century and did not exist in Tudor En- gland.58 It does not appear in the King James Bible (it does appear in other versions of the Bible) or in the Book or Mormon, and the objects designated “brass” were most likely the tin-copper alloy.
The brass plates of Laban may have been copper, as bronze is harder and more difficult to engrave upon. The Liahona may well have been of supernatural origin and, hence, of any metal or alloy that Nephi chose to call “fine brass.”
Pure copper can be “work hardened” by hammering and annealed by heating and slow cooling to prevent cracking with repeated hammering.59 The tin-copper alloy was far superior, however, and bronze was the metal of choice throughout long periods of human history. The Bronze Age in the Near East began well before 3000 B.C. and lasted through 1200 B.C., when bronze was largely replaced by iron.60 Even in the Roman period, however, spearheads and arrowheads (socketed items) were still cast in bronze,61 as iron could not be melted and cast.
“Classical bronze” contained about 10 percent tin, but even 2 percent tin produced noticeable positive effects.62 Tin is rare in the Near East, and the sources of tin for the Bronze Age are still speculative. Tin was quite possibly the catalyst for international trade, bringing tin from Italy, Sardinia, Greece, Crete, Portugal, Brittany, Spain, and faraway Cornwall (British Isles) in the west63 and from Afghanistan, via the Indus Valley, in the east. By the mid-third millennium, native gold and cassiterite (Sn02) were panned together from Himalayan riverbeds and transported to markets in the Near East.64
In the New World some arsenic-rich copper minerals of Peru and Chile may also have been smelted to produce accidental arsenic-copper, but deliberate addition of arsenic is apparent by at least 1000—1700 A.D.65 The placer cassiterite from Bolivia66 provided tin for the tin-copper alloy, characteristic of a much earlier Bronze Age in the Old World; and among the Incas, bronze was a rather common metal available to people of many social classes.67 From the Andes, metal technology appears to move north into Panama and Mexico.68 Spanish conquerors, however, found the Aztecs of Mexico still in a prebronze age,69 a considerable regression from an earlier civilization. The last mention in the Book of Mormon of working iron, copper, brass, and steel is Jarom 1:8, scarcely 200 years after Nephi arrived in the New World. About 250 years later, however, King Noah taxed all people who possessed these metals (see Mosiah 11:3). Roper notes only fire-hardened, wooden weapons, some lined with obsidian chips, in Mesoamerica at the time of the Spanish conquest.70
Lechtman appears to say that the traditional sequence of Near East metallurgy from simple native metals to complex copper alloys to iron-steel does not seem to apply in the New World, where the sequence is related rather to the ideology, worldview, and values of its people.71 That conclusion will need to be verified by further research and discovery, which may also shed light on the extent to which the highs and lows of New World metallurgy were determined by the influx of foreign migrations bringing new technology and by subsequent social decay and loss of technology.
Notes
- See Lynn M. Hilton and Hope A. Hilton, In Search of Lehi’s Trail (Salt Lake City: Deseret Book, 1976).
- See Warren P. Aston and Michaela K. Aston, In the Footsteps of Lehi: New Evidences for Lehi’s Journey across Arabia to Bountiful (Salt Lake City: Deseret Book, 1994).
- See Richard Wellington and George Potter, “Nephi’s Ship: The Key to Identifying the Place Bountiful,” unpublished MS, 1999.
- See Robert P. Whitcome and George Potter, “The Bedouin Bee,” Ararnco World Magazine, March-April 1984.
- Hugh W. Nibley, Lehi in the Desert (Salt Lake City: Bookcraft, 1952).
- See S. Kent Brown et al., “Planning Research in Oman: The End of Lehi’s Trail,” Journal of Book of Mormon Studies 7/1 (1998).
- See ibid.
- See L. Casson, The Periplus Maris Erythraei (Princeton: Princeton University Press, 1989); and W. Phillips, Unknown Oman (New York: David McKay Co., 1996).
- See L. Casson, The Periplus Maris Erythraei.
- K. Arita and M. Nishiie, “Report on the Geological Survey of the Sultanate of Oman” MS on file, Tokyo, Japan, International Cooperation Agency and Metal Mining Agency of Japan.
- See L. Casson, The Periplus Maris Erythraei.
- R. F. Tylecote, A History of Metallurgy (London: The Metals Society, 1976).
- See Jane C. Waldbaum, “The First Archaeological Appearance of Iron and the Transition to the Iron Age,” in The Coming of the Age of Iron, ed. Theodore A. Wertime and James D. Muhly (New Haven: Yale University Press, 1980).
- See ibid.
- See ibid.
- See ibid.
- Dennis Heskel and Carl C. Lamberg- Karlovsky, “An Alternative Sequence for the Development of Metallurgy,” in The Coming of the Age of Iron, ed. Wertime and Muhly.
- See The Interpreter’s Dictionary of the Bible (Nashville: Abington, 1962), s.v. “iron”; Carl G. Johnson and William R. Weeks, Metallurgy (Chicago: American Technical Society, 1977); J. Gordon Parr, Man, Metals, and Modern Magic (Cleveland: American Society for Metals, 1958); and Tylecote, Metallurgy.
- See James D. Muhly, “Mining and Metalwork in Ancient Western Asia,” in Civilizations of the Ancient Near East, ed. Jack M. Sasson (New York: Charles Scribner’s Sons, Macmillan, 1995).
- See ibid.
- Johnson, Metallurgy; and Parr, Man, Metals, and Modern Magic.
- See John Bright, A History of Israel, (Philadelphia: Westminster Press, 1981).
- See James D. Muhly, “Metals,” in The Oxford Encyclopedia of Archaeology in the Near East, ed. Eric M. Meyers (New York: Oxford University Press, 1997).
- See ibid.
- See Heskel and Lamberg-Karlovsky, “Development of Metallurgy”; Johnson and Weeks, Metallurgy; and Muhly, “Metals.”
- See John L. Sorenson, Metals and Metallurgy Relating to the Book of Mormon Text (Provo, Utah: FARMS, 1992).
- See Tylecote, History of Metallurgy.
- Matthew Roper, “Swords and ‘Cimeters’ in the Book of Mormon,” Journal of Book of Mormon Studies 8/1 (1999): 34-43.
- Heather Lechtman, “The Central Andes: Metallurgy without Iron,” in The Coming of the Age of Iron, ed. Wertime and Muhly.
- See Muhly, “Metals.”
- See Johnson and Weeks, Metallurgy.
- See ibid.; and Parr, Man, Metals, and Modern Magic.
- See Johnson and Weeks, Metallurgy; and Muhly, “Mining and Metalwork.”
- See Johnson and Weeks, Metallurgy; and Parr, Man, Metals, and Modern Magic.
- See James W. Evans and Lutgard C. Dejonghe, The Production of Inorganic Materials (New York: McMillan, 1991).
- See Muhly, “Metals.”
- See Parr, Man, Metals, and Modern Magic.
- See Muhly, “Mining and Metalwork.”
- See Parr, Man, Metals, and Modern Magic.
- See Muhly, “Mining and Metalwork” and “Metals.”
- See ibid.
- See Interpreter’s Dictionary of the Bible, s.v. “copper”; and Muhly, “Mining and Metalwork.”
- See Sorenson, Metah and Metallurgy.
- See Lechtman, “Metallurgy without Iron.”
- See ibid.; and Heather Lechtman, “Issues in Andean Metallurgy,” in Pre- Columbian Metallurgy of South America, ed. Elizabeth P. Benson (Washington, D.C.: Dumbarton Oaks Research Library and Collections, 1979).
- See Tylecote, History of Metallurgy.
- See Lechtman, “Metallurgy without Iron.”
- See Muhly, “Metals.”
- See Heskel and Lamberg-Karlovsky, “Development of Metallurgy”; and Muhly, “Mining and Metalwork.”
- See Muhly, “Mining and Metalwork.”
- Funk and Wagnalls New Standard Bible Dictionary, s.v. “metals—copper”; and Interpreter's Dictionary of the Bible, s.v. “bronze.”
- See Muhly, “Metals.”
- See Muhly, “Mining and Metalwork.”
- See Roland W. Brown, Composition of Scientific Words (Baltimore: Brown, 1954).
- The Barnhart Concise Dictionary of Etymology, ed. Robert K. Barnhart (New York: Harper Collins, 1988), s.v. “brass,” “bronze”; and Ernest D. Kline, A Comprehensive Etymological Dictionary of the English Language (London: Elsevier Publishing Co., 1966), s.v. “brass.”
- The Oxford English Dictionary, 2nd ed., s.v. “bronze,” “brass.”
- Interpreter’s Dictionary of the Bible, s.v. “copper.”
- Barnhart Concise Dictionary of Etymology, s.v. “bronze.”
- See Lechtman, “Metallurgy without Iron”; and Muhly, “Metals.”
- See Evans and Dejonghe, Production of Inorganic Materials.
- See Muhly, “Metals.”
- See Lechtman, “Issues in Andean Metallurgy.”
- See Muhly, “Mining and Metalwork.”
- See ibid.; and Muhly, “Metals.”
- See Lechtman, “Metallurgy without Iron.”
- See ibid.
- See Lechtman, “Issues in Andean Metallurgy.”
- See Lechtman, “Metallurgy without Iron.”
- See Tylecote, History of Metallurgy.
- See Roper, “Swords and ‘Cimeters.’”
- See Lechtman, “Issues in Andean Metallurgy”; and “Metallurgy without Iron.”
Subject Keywords
Bibliographic Citation
Terms of use
Items in the BMC Archive are made publicly available for non-commercial, private use. Inclusion within the BMC Archive does not imply endorsement. Items do not represent the official views of The Church of Jesus Christ of Latter-day Saints or of Book of Mormon Central.